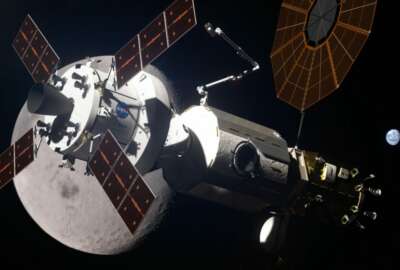
The Johnson Space Center’s Engineering Directorate has its hands full as NASA begins to ramp up toward a new era of spaceflight and exploration.
The Johnson Space Center’s Engineering Directorate has its hands full as NASA begins to ramp up toward a new era of spaceflight and exploration. Among other projects, the Space Launch System’s Orion space capsule will be undergoing its first flight test in April and NASA’s Commercial Crew program, which partners with Boeing and SpaceX, will begin demo flights soon after.
“I’ve been here 30 years, and I’ve never seen this much volume of work of different kinds coming through the center,” said Julie Kramer White, deputy director of engineering at NASA. “To be able to support this many different programs that are this close to flight — you have to appreciate that a year or two years in aerospace timelines is very fast.”
On top of the high tempo work for these near-term deadlines, they also provide support for a number of other currently existing NASA missions.
“Probably the one most people know about is the International Space Station,” White said. “Continuously manned in orbit now for about 15 years, we provide engineering support across all kinds of disciplines of engineering to the international space station program to keep their systems up and functioning every day to support the crew.”
And they drive development for future programs as well. For example, White said her team is responsible for precision landing capabilities for lunar landings. They’re also developing in situ resource utilization capabilities — how air, water and other consumables are used and replaced over long-term missions — for potential Mars missions.
These missions can draw from every discipline of engineering, White said. Aerospace, material and mechanical engineering are the most obvious, but electrical and software engineering are just as important for making sure the systems work aboard spacecraft. And in situ resource utilization requires a blend of chemical engineering alongside mechanical and material.
For example, the life support systems on the Orion capsule had to be upgraded, since they’re intended for much longer missions.
“So Apollo was out to the moon and back in a relatively short period of time. We talk about missions that are pushing over three weeks, sometimes even more,” White said. “So the systems provide the same functions, but in [Apollo’s] case tended to be consumable systems, where you carried a limited amount of assets. In our case they tend to be regenerative.”
That includes generating power through solar arrays, and replenishing the atmosphere through the use of a scrubber that separates contaminants and ejects them into space.
That’s not the only upgrade; while the Orion borrows heavily from concepts used in the Apollo program, many improvements have been made around the technologies and processes.
“Our airframe has a lot of similarities to advancements that have been made in aircraft,” White said. “So you see much more use of composites, much more use of advanced alloys. The airframe is fundamentally aluminum, in this case, which is similar to what Apollo was, but the manufacturing techniques are totally different.”
The new techniques fuse the vehicle together with much more strength. And the tiles on the back shell of the Orion, White said, while derivative of those used on the Space Shuttles, have gotten tougher, but are still just as light.
One of the main things Orion borrows directly from the Apollo spacecraft is its shape. The geometry is similar, though Orion is about 50 percent bigger, White said.
“What that did was that allowed us to, rather than starting from scratch with a different shape of vehicle, that allowed us to leverage a lot of the flight data that came out of Apollo as a starting point for being able to work Orion,” she said.
And that’s what the upcoming flight test in April is all about — gathering data to determine the margins for a human spaceflight mission.
“It will see all the environments that the actual human missions will see, and it allows us to check all of the analysis and assumptions and models,” White said. “And the performance — a big aspect of it as well is reentry performance, and looking at how the heat shield performs under this kind of reentry velocity. Going out to the moon, you come back at a lot higher velocity than you do when you’re just orbiting the Earth. So the heat shield is obviously very critical in this application, and this is the biggest, highest velocity, highest energy we’ve ever attempted.”
Copyright © 2024 Federal News Network. All rights reserved. This website is not intended for users located within the European Economic Area.
Daisy Thornton is Federal News Network’s digital managing editor. In addition to her editing responsibilities, she covers federal management, workforce and technology issues. She is also the commentary editor; email her your letters to the editor and pitches for contributed bylines.
Follow @dthorntonWFED