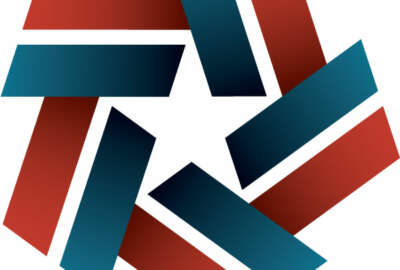
How one federal manager moved his co-workers to telework, shifted his hours and supervises his team of eight remotely during the pandemic.
Best listening experience is on Chrome, Firefox or Safari. Subscribe to Federal Drive’s daily audio interviews on Apple Podcasts or PodcastOne.
The coronavirus pandemic has changed almost everything about the nature of work.
It’s no different for Vince Stamper, who’s responsible for a team of eight people at the Trident Refit Facility Bangor in Washington state. Before the pandemic, telework had been a relatively foreign concept.
His agency wasn’t accustomed to telework, he said. Of his command of 1,800 people, just one employee had a telework arrangement for medical reasons.
Industrial shipyards like his can’t naturally shift to remote work.
“The instructions were in place,” said Stamper, who’s also the region 4 director for the Federal Managers Association. “The logistics to scale were not in place. Our IT department has really been working over time to make this happen.”
It hasn’t necessarily been easy.
Moving to telework forced Stamper to shift his typical hours — mostly to accommodate his employees’ new schedules who are dealing with family or personal stress during the pandemic.
“I basically split my day into two halves, a morning and an evening, just because the team has different needs,” he said. “I have some employees who have special needs children who are at high-risk, so they need to be providing day care basically in the middle of the day. Connectivity and bandwidth is an issue in the middle of the day, so I have some people who are splitting their shifts because of that.”
Stamper said his senior leaders were quick, even before stop-move orders had been issued in the area, to make arrangements for the workforce.
“My agency and my organization supports some pretty critical mission needs,” he said. “They very quickly identified who was absolutely essential to be there on the deck plate, who we could not put on telework, and get the people who could telework and get them out of the mix so we could minimize exposure.”
One of Stamper’s employees has a son home from preschool. Another co-worker has an elderly dependent at home.
“That definitely is presenting some real stress for all those individuals,” Stamper said. “Not only are they dealing with the stress that goes with the situation that they’re in, but they’re very concerned about their family members. They’re very concerned about the people that they’re primary caregivers for.”
The shift to telework has been a positive one in a sense, Stamper said. He’s connecting with some of his employees, especially those who worked in a different building from him, more often now than ever before through FaceTime and other video platforms.
The current environment has also forced Stamper to become more flexible and creative, traits that don’t often naturally mix with bureaucracy, he said.
“The nature of the work that I do… is all about finding really creative solutions. Having done that for many years and having a personality that really fits with that, I was always kind of a square-peg in a round hole in a military environment,” he said. “In this situation that has become a real asset.”
Tapping into that creativity has allowed Stamper and his team to focus on their mission, which has evolved during the current pandemic.
His shipyard is one of at least four others across the country that has started 3D-printing personal protective equipment and other safety devices.
“We have this industrial capacity that supports our mission at sea,” Stamper said of the 3D printing work. “But we also can use that productive capacity to meet challenges like this.”
Printing PPE for his local shipyard is the first priority, Stamper said, and his team is exploring how it can share those materials with local health care systems.
“There’s a lot of 3D print production out there, everything from splitters so that you can use a respirator for two patients, to something as simplistic as a face shield or a face mask that’s reusable,” Stamper said. “Those are the things that we’re coordinating.”
Stamper and his team are using a collaboration tool that allows his shipyard to coordinate production and best practices with the others. Many of the 3D print files are all open-source, so Stamper and his team can review one and modify it for their own needs.
“There’s an attachment you can put on a door so you don’t have to use your own hands to open the door; you can use your foot,” he said. “It attaches down in the lower corner of the door. We found an open-source file to do that, and since then we’ve modified that file to make it more robust and easier to use on the industrial-type doors that are within our command.”
For Stamper, 3D printing is a passion. He’s planning to make his own models in his spare time using the 3D printer his son built for him for Father’s Day.
Stamper said he’ll share the successful models with his 3D printing community. He’s hopeful the current environment will inspire others to be more open and collaborative, as it has for him.
“Act in a way that you will be proud of when this is all said and done,” he said. “Reach out to your community. Reach out to your neighbors. Look for capabilities within your professional life and your personal life where you can add value to those networks and to those communities.”
Copyright © 2024 Federal News Network. All rights reserved. This website is not intended for users located within the European Economic Area.
Nicole Ogrysko is a reporter for Federal News Network focusing on the federal workforce and federal pay and benefits.
Follow @nogryskoWFED