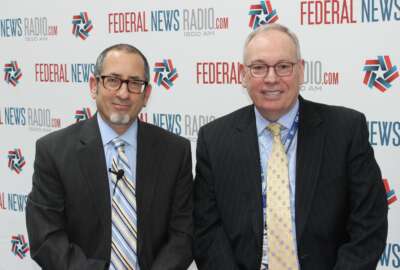
Two pilot projects, both using existing data to improve NAVSUP's business processes, are expected to produce results by August.
To listen to On DoD on your phone or mobile device, subscribe on PodcastOne or Apple Podcasts. The best listening experience on desktop can be found using Chrome, Firefox or Safari.
As with many other federal organizations, Naval Supply Systems Command is not suffering from a lack of data. But the information it holds about its responsibilities to move food, parts and supplies around the world tends to be unstructured, trapped in legacy IT systems and not always used on a day-to-day basis to help the command make better business decisions.
NAVSUP is exploring ways to change that via a pair of prototype programs, both focused on the way the command does its contracting. Both, under the banner of an initiative it calls its “digital accelerator,” are underway now, with initial results expected by August.
In the first, it’s attempting to employ a technique called robotic process automation to help reduce the time it takes to answer vendors’ questions and move various documents back and forth during the process of procuring supplies for the fleet.
“What we discovered as we dug into that was that there were delays that had to do with how the information got processed through email,” said Kurt Wendelken, NAVSUP’s chief information officer and assistant commander for supply chain technology. “So, say a contractor comes in looking for answers to a question: we probably already have answers to those questions prepared, and by using this kind of system, it will automate a lot of those functions and thus speed up the process. It’s looking very promising that by changing how we answer those things, we can cut quite a bit of time out of our contracting process.”
A second project aims to improve the process the Navy uses for moving what it refers to as “depot-level repairable” items around the world. Generally, when components of ships, aircraft and other weapons systems break down, they’re moved back to U.S.-based facilities to be repaired and refurbished before returning to the fleet.
The overhaul of those parts is one of NAVSUP’s primary responsibilities, but as of now, the path they take between overseas deployed locations and U.S. depots tends to be circuitous and inefficient.
To design a more logical logistics chain, the command intends to build software applications that leverage the data it already has about depot-level repairables. It’s set an August target to develop minimally-viable products for both the shipping and contracting projects, but is redesigning its business processes in tandem, Wendelken said.
“As someone who’s done IT for 29 years inside the Navy, I would tell you that the IT itself is almost never the problem,” he said. “It’s always the business process. There are some that the Navy controls and some that are dictated by law. But, in these specific areas we can control, we’re working to change them. The shipping initiative is going to require a partnership between us and [the Defense Logistics Agency], and we’re already in conversation with them about how we make that work for both of us, because DLA plays a substantial role.”
To pick the initial candidates for the digital accelerator, NAVSUP hired an outside firm, Boston Consulting Group, to scrub its existing business practices and look for opportunities for improvement. The company identified roughly 100 areas in which it thought the command could make itself more efficient.
But those ideas came as much from the NAVSUP’s own employees as from the consultants’ expertise in management reform.
“This was entirely driven by their engagement with our workforce,” Wendelken said. “[Boston Consulting] uses the term ethnographic research, which really just means that they went around and talked to people and asked, ‘Hey, how’s your job going? Where are your challenges? What do you think you could do if you had the power to make your job better?’ Every one of these initiatives … are really things that our workforce knew, and Boston Consulting just showed us how to extract those ideas and information from our workforce.”
Then, to settle on the first two digital accelerator prototypes, NAVSUP created a “shark tank” process, inviting groups of employees who believed they had a solution to a particular problem to present them to the command’s leadership in successive rounds of competition.
Wendelken said NAVSUP intends to turn the lessons it learned from the Boston Consulting arrangement into an ongoing process that will continue to solicit ideas for improvement, without requiring continuous assistance from management consultants. The command has created a dedicated program office that will apply similar techniques to solve its problems itself.
“That’s been a big part of this effort: teaching our own folks about how to investigate these problems, because the problems that have been uncovered are problems that people knew about,” he said. “Maybe people didn’t feel empowered to do something about them, but we’re really working hard to change that.”
Copyright © 2024 Federal News Network. All rights reserved. This website is not intended for users located within the European Economic Area.
Jared Serbu is deputy editor of Federal News Network and reports on the Defense Department’s contracting, legislative, workforce and IT issues.
Follow @jserbuWFED