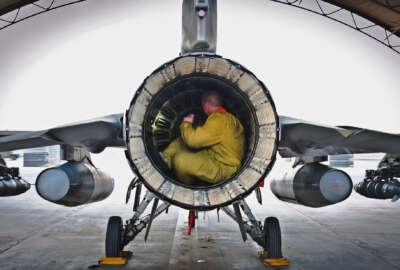
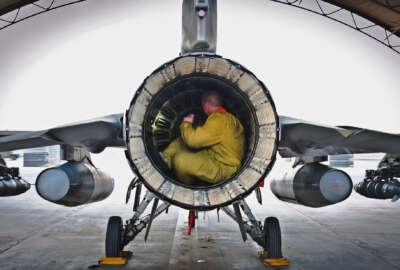
Delta Air Lines reduced its spare parts inventory by $500 million by moving toward condition-based maintenance. The Air Force thinks it can achieve something si...
In April 2018, an Air Force KC-135 tanker landing in Rota, Spain, suffered a failure on one of its hydraulic pumps. No spares were available at the base, so instead of performing its missions the tanker sat on the tarmac for five days waiting for repairs.
That same scenario — involving the same pump — repeated itself two dozen times over the last four years, and the Air Force estimates the downtime costs involving failures of one single part amounted to $6.6 million.
It’s the sort of problem officials think they can now start to put behind them using a practice commercial airlines have been employing for a decade: Condition-based maintenance (CBM). Instead of replacing parts after they’ve failed or relying on fixed schedules, air carriers have figured out that they can predict failures with a high degree of accuracy and get ahead of problems when maintenance makes the most operational sense.
The Air Force and DoD brand their variant “CBM+.” It’s still in its infancy, but officials have high hopes for how it might cut maintenance costs and boost aircraft readiness. The Air Force’s program differs from the commercial ones that inspired it in at least one major respect: Many of the military airframes the service operates are decades old, and aren’t outfitted with the same number and quality of sensors that spit out detailed data about which components are coming due for service.
Because of that, at Air Mobility Command, about 80% of the CBM program will rely on what officials there call Enhanced Reliability Centered Maintenance (eRCM). Instead of depending on data feeds from an individual aircraft’s sensors, algorithms will crunch through detailed records the Air Force already has about how a particular part has historically performed across the fleet — and on a particular airplane — and determine the ideal time to replace or repair it.
The AI algorithms that analyze that data are largely being developed by the Air Force Lifecycle Management Center. AFLCMC is also working on ways the Air Force can take advantage of the performance data it does have from its newer airframes that are outfitted with more modern sensors.
Downs said that sensor data will feed into a separate line of effort — the other 20% of the CBM+ approach — called Predictive Algorithm Development (PAD).
“We’re focusing on eRCM just because it’s going to get us our biggest return on investment, but eventually we will go back to the PAD side, because that completes the holistic view of CBM+,” he said. “But it’s going to be very challenging for some of the aircraft that do not have those onboard diagnostics. The KC-135, for example, was built in the mid-fifties, so there’s not a lot of bells and whistles on that aircraft. But what we can do is look at things like the flight data recorder that’s typically used for safety investigations. We’re looking for some things that we may be able to tie back to the maintenance side.”
And even on some of its newer platforms that are outfitted with sensors, the data they collect is often encoded or encrypted by the original equipment manufacturer, because the Air Force wasn’t thinking about CBM at the time it signed the acquisition agreements for those systems.
But now that the service is starting to get a better handle on what sorts of data are useful for maintenance purposes, it’s beginning to use those lessons to inform its intellectual property policies on the front-end of the acquisition process.
“Right now we’re in some significant conversations with the B-21 program about things that they need to be writing into their contracts as the aircraft is developed to capture all of these lessons learned,” Downs said. “And as we go through some of our other platforms, as contracts come up for renewal with our OEM partners, we’re having those same conversations just to make sure that we’ve got on-ramps and off-ramps going through as CBM+ matures over the next number of years.”
The Air Force’s gradual move toward condition-based maintenance also has major implications for its supply chain.
On one hand, the government and industry systems and processes that deliver parts to where they’re needed will have to adjust to a cadence that ensures they are ready to install well before they’ve failed.
But if all goes according to plan, it also means the Air Force and Defense Logistics Agency will be able to reduce the total number of spare parts they keep on hand just in case of unexpected problems.
“Our data point for this is Delta Air Lines,” said Brig. Gen. Steven Bleymaier, AMC’s director of logistics, engineering and force protection. “They were able to reduce or remove $500 million from their supply inventory by better predicting failures and reducing that ‘just in case’ inventory. So we would expect to see similar results in the Air Force supply system as we are able to pinpoint where we need parts, when we need them.”
Copyright © 2024 Federal News Network. All rights reserved. This website is not intended for users located within the European Economic Area.
Jared Serbu is deputy editor of Federal News Network and reports on the Defense Department’s contracting, legislative, workforce and IT issues.
Follow @jserbuWFED