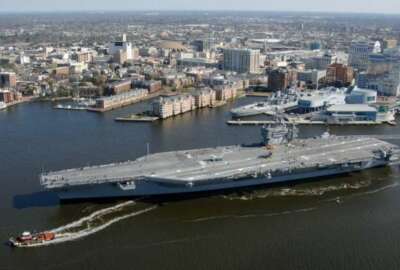
Norfolk Naval Shipyard is working on a priority list and a 20-year plan to begin upgrading its facilities, including buildings that date back to the 1830s, and...
Norfolk Naval Shipyard just celebrated its 251st birthday, which means it’s been in existence longer than the country it serves. But some of its facilities are nearly as old as its legacy.
Capt. James “Jip” Mosman, acting commander and production resources officer, said it has buildings that date back to the 1830s, and equipment from the World War II era. That’s why it’s working on a priority list and a 20-year plan to begin upgrading its facilities.
Norfolk Naval Shipyard is one of the Navy’s four public shipyards — along with Pearl Harbor, Portsmouth and Puget Sound — that have full fleet service capability, which means they can service any ship in the fleet, including refueling nuclear submarines and aircraft carriers. But destroyers and other smaller ships go elsewhere for service because those are processes that take multiple years, so they tend to be the focus of the public shipyards.
“Essentially, the nuclear material is removed and replaced with new material,” Mosman told the Federal Drive with Tom Temin. “Meanwhile, while that’s going on, the ship is also modernized, refurbished, new equipment is installed, and updates to various systems are all done.”
It’s highly specialized work, requiring a great deal of training and precision, Mosman said. It’s carried out by a combination of civilian and uniformed personnel, though most of the work is done by civilians. Norfolk Naval Shipyard only refuels submarines, Mosman said. Aircraft carriers are handled elsewhere.
But while a ship is being serviced, depending on where it is in the lifecycle, it may get put into dry dock. That may happen so the shipyard can clean and paint the hull, repair corrosion, and possibly even maintain the propeller.
Meanwhile, the crew continues working aboard the ship. Mosman said they have their own maintenance to handle, which is not as deep or detailed as what the shipyard performs, but can also involve learning about upgrades the shipyard is performing.
This is all handled “on availability,” which means during a scheduled point in their lifecycle. The shipyards have a staff of engineers that note when certain classes of ships tend to have the same issues at the same points in their lifecycles. That information informs the activities of the shipyards, but it’s also sent back to the contractors so it can be taken into account in future designs.
But these shipyards are also available if an unforeseen event occurs, like a collision.
“If there was some type of situation where we need to do unplanned maintenance, we work with our fleet operations side and the maintenance side and we determine what docks are available,” Mosman said. “We go do assessments and determine how much time it would take to repair, what effort is going to be required. And then we, as a team with the fleet and NAVSEA [Naval Sea Systems Command], we work out where and when it’s going to go in the dock and then we go and execute that evolution.”
Mosman said the shipyards are also attempting to encourage innovation among their employees, providing an innovation lab to develop their ideas.
“They are bringing in state-of-the-art things such as additive manufacturing; virtual, augmented or mixed reality; robotics; laser ablation,” Mosman said. “And they are bringing that technology in, exciting technology from out in industry, and helping us to integrate that into the work we do here. We also have a rapid prototype center, which is an area where our employees — because nobody knows how to make something better than the guy on the deck actually looking at it — he comes up with an idea, he goes to the rapid prototype center, and the folks in there help him bring that idea to reality. So we innovate on the move there as well.”
Copyright © 2024 Federal News Network. All rights reserved. This website is not intended for users located within the European Economic Area.
Daisy Thornton is Federal News Network’s digital managing editor. In addition to her editing responsibilities, she covers federal management, workforce and technology issues. She is also the commentary editor; email her your letters to the editor and pitches for contributed bylines.
Follow @dthorntonWFED