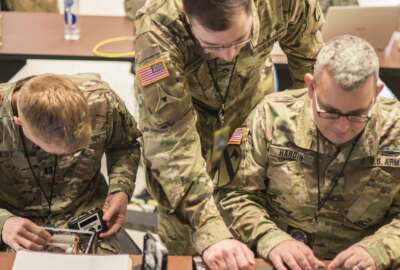
The Army's acquisition shop has enlisted the service's expeditionery technology search group to help with the rapid production of low cost ventilators.
Best listening experience is on Chrome, Firefox or Safari. Subscribe to Federal Drive’s daily audio interviews on Apple Podcasts or PodcastOne.
The Army’s acquisition shop has enlisted the Army’s expeditionery technology search group to launch a challenge competition. It’s goal: Rapid production of low cost ventilators to help the military stay on top of COVID-19 cases. For details, Federal Drive with Tom Temin spoke with the director of laboratory management in the office of the Assistant Secretary of the Army for Acquisition, Logistics and Technology, Dr. Matt Willis. And director of the office of medical systems Col. Matt Clark, also in ASALT. You hear Willis first.
Interview transcript:
Dr. Willis: The goal here is to identify new technology solutions for ventilators that can be used in field hospitals where there is not necessarily the established infrastructure that you might commonly find in, you know, hospitals. So for instance, a technology that can work off of generator power or dirty energy, or, you know, for instance, places where you might not have hospital grade oxygen under pressure. So it’s really about trying to develop a solution quickly, you know, in a quick turn because we recognize this is a exigent challenge to the country and the world to develop a solution that then we can, you know, potentially use in field hospitals that are being stood up across the country, or also potentially deployed across the world support our troops stationed across the globe.
Tom Temin: And Colonel Clark, I guess I’m a little surprised this is coming up now. I mean, obviously, the coronavirus is a threat to everyone, including military troops. We’ve had a sailor unfortunately die of it from the USS Roosevelt. But given the way the army prepares to operate in austere conditions, how come this didn’t come up years ago with a need for this type of equipment that can operate on dirty power and etc?
Colonel Clark: That’s a really good question, sir. The short answer is really it relates back to the ability to get the products that we need at the scale we need. The reason this is coming up now, in my opinion, anyway, is that as we take a look at the scale of the problem, this is global pandemic, we haven’t had something like this at least in certainly modern memory. And so the scale of the problem has the capability or the ability to go beyond what systems and kits that we have in our formations today. And since we were able to meet that need, we didn’t have this as a challenge. But now we see through this particular case, that the challenge can really not only energize military technology needs, but also on the civilian side.
Tom Temin: And you are choosing the route of a challenge contest. And that sounds like maybe a lack of confidence in the existing industry, whoever I don’t know anything about the ventilator industry, but to adapt existing products, say with different power supplies, for example, with a switching power supply that runs on USB or I’m just making it up, as opposed to going to all new or possibly finding brand new players explain that strategy.
Colonel Clark: The first part is what is interesting here, if you look again across history, the great thing about ventilation is, mechanical ventilation, is there has been a need for mechanical ventilation for over 100 years. And if you look at the points where you have an inflection or you have a change in the technology that we’ve been able to bring to bear, it is brought about because of that demand signal. So up into the late 1920s, there’s this push for this negative pressure, ventilation, negative and that’s when you get in late 1920s, you get the iron lungs. And then this keeps pushing forward to the end of the 1950s. And they start to realize, well, these big bulky iron lungs are maybe a bit too much. So really what we need is maybe positive pressure ventilation. That’s where you start to get in the kinds of ventilation we do today in most of our hospitals and intensive care units, that is in the 1950s. And so each of these situations, there’s either an epidemic or an outbreak. Here we have an outbreak with COVID-19. This provides another opportunity where a challenge, which is somebody thinking in a different way that you can really take advantage of the opportunities that can be around quality, or I’m sorry, around capability, the design that is it, can be around the cost or it could be around manufacturing. So these are all great opportunities for us to take advantage of right now.
Dr. Willis: So what I would add is that, you know, the, the construct behind using a challenge competition doesn’t necessarily reflect a lack of confidence in current industry, but I think, rather reflects the Army’s desire to be aggressive, to lean forward, to realize that this is a challenge for of course, our troops, but the country at large and to try to identify, as Colonel Clark mentioned, novel solutions, be it ideas or manufacturing processes, or new concepts entirely, be able to quickly move to identify these solutions. Evaluate the potential for a prototype, and then move towards FDA regulatory requirements so we can rapidly develop and field these solutions.
Tom Temin: And just let me ask a parallel question. Recently, the government had a big challenge, it’s still going on with respect to dialysis, just to make a parallel. And one of the issues with dialysis is that the machinery and the procedures haven’t really changed much in decades. And they’re dangerous and cumbersome with respect to ventilation. Is this something that’s kind of due for a, maybe a revolution anyway, as earlier you said when the iron lung went out of fashion and the positive ventilators came in. Are they pretty much the same as they were with the same dangers and requirements as they were 30-40 years ago?
Colonel Clark: No actually. So there’s been movement and positive directions for how they do ventilation Ever since then, they’ve got new controls and new challenges that they’ve been able to address. And there’s still a robust area of research for the medical scientists in the group, they can go out and look and see where some of these sort of state of the art ideas have been explored in terms of adding new variable controls for positive expiritory pressure, for pressure regulated volume control. These are some of the things that have have come about. But the other areas that haven’t necessarily come in, quite honestly is the area of how you can develop a high quality, high reliability system at a lower cost on a shorter timeline. That’s one of the challenges. These ventilators that you will see in a hospital today, you’re talking about 10s of thousands of dollars. So small hospital out in rural Iowa, for example, would only have a couple Have them. And that’s probably due to cost and cost is related to this high reliability factor that you need. And that’s getting built in. And that’s one of the great things that actually the FDA is leaning forward on, which is you build in some of that quality. And some of that’s coming along as this process progresses. What we haven’t necessarily seen for that 10s of thousands of dollars, can you do it for less? Can you use the new innovations that are occurring in manufacturing, whether it’s precision manufacturing or additive manufacturing or something with micro electronics? That’s a question we just haven’t asked because there hasn’t been the demand signal.
Tom Temin: And how does the challenge contest work? And what are some of the deadlines and what types of companies you’re expecting to join in?
Dr. Willis: The challenge contest is executed under Title 10, Section 2374 A, and it really, basically allows the Department of Defense to put out a challenge statement. So a problem statement and allows entities across the US so to include small businesses, large businesses, innovators that might be working out of their garage, or universities, etc, to pose solutions to this problem statement, and we make it really, really easy. So in terms of posing a solution, we just ask companies to put together a quad chart with their idea and optionally submit a video that might demonstrate a prototype or where their briefing their idea, they submit it to our our website. And with this particular challenge statement, this particular variant, we have an open proposal call and the submissions are reviewed as they are received. So they’re reviewed not only by our experts, but also by subject matter experts in industry and academia. And we also actually have some doctors in hospitals across the country really looking at these technologies, seeing are they innovative, and can they fit our needs. So if the technology is deemed potentially viable, we provide a $5,000 prize to these companies, an opportunity to come and actually do a virtual pitch to our panel of subject matter experts. And once we have that pitch, a select number of companies will get $100,000 Prize. And they’ll use that money as sort of seed money to either develop a working prototype, to work out supply chain logistics analysis, and really lean forward so that we can, you know, potentially get a contract in place to work through FDA regulatory challenges and get into a low rate production of these ventilators.
Tom Temin: Matt Willis, Director of laboratory management in the Office of the Assistant Secretary of the Army for Acquisition Logistics and Technology. And you also heard from the Director of the Office of Medical Systems Colonel Matt Clark.
Copyright © 2025 Federal News Network. All rights reserved. This website is not intended for users located within the European Economic Area.
Tom Temin is host of the Federal Drive and has been providing insight on federal technology and management issues for more than 30 years.
Follow @tteminWFED