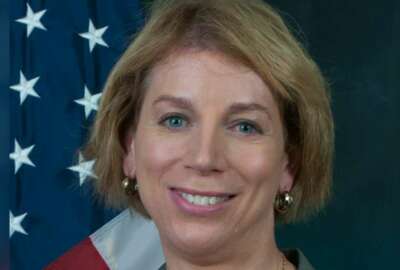
The Navy demonstrably accelerated shipyard maintenence in 2020, but still won't meet its goal of zero delays in 2021.
The Navy made major progress toward eliminating maintenance delays in its shipyards in the fiscal year that ended Sept. 30, partly by setting more realistic goals for how long each period of upgrade and repair work would actually take.
In fiscal 2020, the total number of days by which ships overran their planned maintenance schedules fell by 80% compared to the previous year, according to the top official at Naval Sea Systems Command (NAVSEA). In 2019, there were a collective 7,000 days of delays across the fleet. That fell to about 1,100 by last year.
“We did a fairly detailed analysis on availability duration and whether we were planning the duration of the availabilities correctly up front, and what we found is we were not doing that,” Vice Adm. William Galinis, NAVSEA’s commander told reporters Thursday. “We had a lot of data that showed us that after we went through and did the analysis. And after we reset the duration for availabilities going forward, that’s going to help us tremendously.”
But the 2020 gains were not purely a matter of moving the goalposts. Galinis said the Navy and its contractors truly are getting ships in and out of their maintenance periods more quickly than in years past. Even when compared against the earlier, unadjusted schedules, the number of days of delay in 2020 still would have been down by 40%, compared with 2019.
After a major hiring initiative in the late 2010s, the Navy had set a goal of eliminating maintenance delays completely by fiscal 2021. Galinis said it’s now clear the service won’t achieve that goal, but that’s mainly because of a few especially-difficult maintenance problems on a relative handful of ships.
The guided missile destroyer USS Oscar Austin, for example, was badly damaged in a 2018 shipyard fire, and repairs are taking longer than expected. And four Ticonderoga-class cruisers that require extensive upgrades to their electronic, hull and mechanical systems to stretch them to their planned 35-year service life are proving to be more complicated than originally planned.
“We’re not going to make the goal we set for ourselves, but we understand the discrete drivers behind that,” Galinis said. “That’s not to say there won’t be other ships that are that are out there, and we’ll continue to manage that, but overall, right now, we’ve got about 67% of our avails tracking to on-time delivery. That’s up from less than 50% last year. So I think we’re moving the needle in the right direction.”
The Navy’s persistent inability to process its ships through maintenance yards on time has been highlighted for years in independent watchdog reports. The Government Accountability Office argues — and the Navy generally agrees — that the problem poses serious readiness issues, since it consistently causes fewer ships to be available to military planners than they expect.
According to GAO, 75% of ships that entered a maintenance yard stayed there for longer than they were supposed to between 2014 and 2019. As recently as 2019, more than half of the delays lasted for longer than 90 days. GAO said the primary issues are insufficient capacity at the Navy’s public and private shipyards and a shortage of skilled personnel.
But NAVSEA has hired thousands of new workers over the past several years to help tackle the workforce problem. Galinis said training programs for that new cadre of shipyard employees is proceeding well, despite the challenges of COVID-19.
In the meantime, the command is looking to solve other problems that have tended to slow down the maintenance process.
One way is to minimize the amount of new, unplanned work that’s ordered after a ship has already gone into its maintenance period.
“It’s been almost case-by-case, ship-by-ship, in terms of how we’ve been doing this. But our [Surface Maintenance Engineering Planning Program] has done a really good job of building and stabilizing the class maintenance plan — what we refer to as directed work, and we’re trying to push more maintenance work into that directed work category,” Galinis said. “What that does is it really provides a pretty stable baseline in terms of requirements and planning for a larger percentage of the work that we’re doing in an availability.”
In the meantime, Galinis said NAVSEA has been making more of a concerted effort to make sure the materials shipyards need to complete repairs are ready when a ship enters the yard, so that workers aren’t waiting for components to arrive.
“That’s another area that has caused us to go long in some availabilities, where either we didn’t order the material on time, or we ordered it and for whatever reason, the lead times were longer than anticipated,” he said. “We stood up a material group to really get after that.”
Copyright © 2024 Federal News Network. All rights reserved. This website is not intended for users located within the European Economic Area.
Jared Serbu is deputy editor of Federal News Network and reports on the Defense Department’s contracting, legislative, workforce and IT issues.
Follow @jserbuWFED