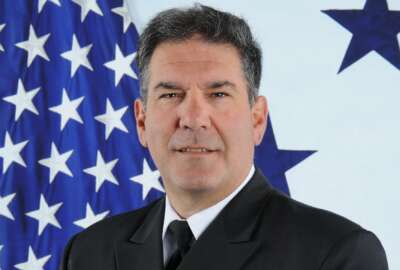
There are a lot of reasons behind maintenance delays in the Navy's shipyards. But one, only recently uncovered, is that most of the supplies artisans need to do...
The Navy is taking several steps to shorten the time it takes to get its vessels in and out of maintenance at its shipyards, including with a huge, multiyear and multibillion dollar program to modernize the yards’ outdated infrastructure.
But as officials dug into the problem of maintenance delays and broader logistics issues, they found at least one other massive contributor that’s arguably easier to fix: getting the parts the Navy’s tradesmen need to do their work at the jobsite at the time the projects begin. Fixing that problem alone could go a long way toward making sure ships’ maintenance availabilities are finished on time.
That’s one of the more potent discoveries the Navy has made as part of a much broader project called Naval Sustainment System-Supply (NSS-S), led by Naval Supply Systems Command (NAVSUP), and in the case of the shipyards, supported by Naval Sea Systems Command (NAVSEA).
Rear Adm. Peter Stamatopoulos, NAVSUP’s commander, said the project’s data analytics showed that, on average, only about 30% of the parts needed to complete a submarine or surface ship’s planned maintenance were available when the vessel entered the yard. And those late-arriving supplies, in turn, are responsible for about 30% of the total delays in ships’ scheduled maintenance periods.
“What happens is that the rest of the material requirements are discovered as that availability is moving along. Some of it is never identified upfront in the planning process, and some of it occurs when they open and inspect a planned job, but what we’ve found is that oftentimes, in that growth work, we should have the parts on hand and ready to go before the work is actually started,” he said during a wide-ranging interview about NSS-S for Federal News Network’s On DoD. “It’s part of the dysfunction that has developed over the course of time — we haven’t been able to be as predictive as we need to be in our requirements determination to support those jobs. But we’re getting after that.”
In the year-and-a-half NAVSUP has been working on NSS-S, the parts availability rate has improved noticeably, to 37%. The objective by the end of the five-year project is 100%, though Stamatopolous acknowledged that’s a stretch goal.
Another discovery Navy officials made as part of NSS-S: the low availability rates have flown under the radar until recently, in part, because local supply departments at each Navy shipyard have tried to solve the missing parts problems by themselves, ordering what they need on their own.
“So requirements were finding their way around the supply system, and not going through a central point,” Stamatopolous said. “And when we don’t go through a central point, we don’t have the demand visibility we need so that we can be more predictive with the material that we should have on hand, either in the shipyard ready to go, or in our wholesale supply system in NAVSUP and the Defense Logistics Agency.”
Going forward, the idea is to minimize the number of instances in which the Navy’s four public shipyards need to order items from vendors separately. NAVSUP is trying to centralize more of those orders through its own supply system to take advantage of the broader Navy’s buying power, apply category management principles, and give its vendors more predictability so that each of its shipyards aren’t, in effect, competing against each other with urgent requests for the same items that could, ideally, have been bought ahead of time and stocked in Navy or DLA warehouses.
Although the shipyard element has been a major focus of the NSS-S initiative, it’s only one of many. Stamatopolous said the bigger project — which ranges from improving NAVSUP’s industry relationships to getting a better handle on cash management in its working capital fund — has achieved about $600 million in verified savings thus far.
And many of the “pillars” of the project are interrelated.
For example, if the Navy can do a better job of forecasting the parts it’ll need for maintenance availability and minimize the amount of local purchasing, NAVSUP is likely to do a much better job of forecasting its demand to vendors.
“One of the things that I continuously hear from them is they would like to have a more stable demand signal,” Stamatopolous said. “We also need to make sure that we have the right mix of organic repair and commercial repair, because we have to preserve and protect both [capabilities], and the best way that we can do that for the commercial base is to give them a solid, stable demand. We have to be sensitive to their needs for cash.”
Meanwhile, the Navy is also starting pilot programs that try not only to minimize the number of cases in which local elements of the Navy’s sustainment system is competing for the same parts, but also the number of instances in which the acquisition portions of the Navy bureaucracy are competing against the sustainment portions for the exact same items.
“What we’re doing in NSS-Supply is bringing both of those disciplines into the room,” Stamatopolous said. “We’re creating RFPs for not only the new procurement of parts, but also the sustainment, and bringing it together. That’s the first time that that’s happened in at least 20 years, and what it allows us to do is bring the full buying power of both the acquisition community and NAVSUP into the same room. We’re negotiating upfront sustainment before we talk about how many numbers of airplanes or components that we’re going to be purchasing. It’s a whole different approach to how we do contracting and acquisition. And it’s exciting.”
Copyright © 2025 Federal News Network. All rights reserved. This website is not intended for users located within the European Economic Area.
Jared Serbu is deputy editor of Federal News Network and reports on the Defense Department’s contracting, legislative, workforce and IT issues.
Follow @jserbuWFED