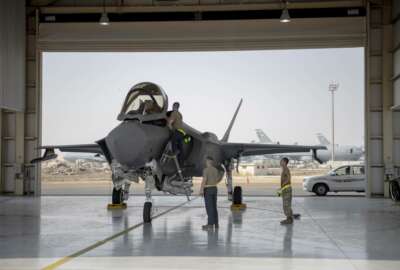
Air Force officials are looking to expand the program under which new equipment is designed completely digitally, and moving to construction without blueprints or...
Best listening experience is on Chrome, Firefox or Safari. Subscribe to Federal Drive’s daily audio interviews on Apple Podcasts or PodcastOne.
Air Force officials are looking to expand the program under which new equipment is designed completely digitally, and moving to construction without blueprints or clay models. It’s already been proven in several programs. And for what’s ahead, Federal Drive with Tom Temin turned to the Air Force’s Deputy Assistant Secretary for Science, Technology and Engineering, Kristen Baldwin.
Interview transcript:
Tom Temin: Ms. Baldwin, good to have you on.
Kristen Baldwin: Hello, thank you for having me.
Tom Temin: Now, tell us more about this program. Because digital design, [computer-aided design] and so forth has been around for quite a number of years. What’s new here for the Air Force?
Kristen Baldwin: I’m so pleased to talk to you today. My office provides guidance and policy for our engineering and science and technology initiatives, including prototyping, experimentation, and digital development. And I wanted to share with you what is digital engineering and how we’re applying it. And so if I could just start real quick by saying digital engineering is really the creation of computer readable models and data to represent all aspects of a system including its components and other systems, it’ll integrate with operational missions, it will support – and integrating all of this into a digital model that can be used as a foundation for our engineering and acquisition activities.
Tom Temin: Give us an example.
Kristen Baldwin: Sure, one of our premier Pathfinder programs is our T-7A trainer aircraft. By embracing modeling and design tools, we have cut assembly hours reduced to 80%. And software development time was also cut in half. The aircraft design was able to move from computers to first flight in just 36 months.
Tom Temin: In other words, the computer aided designs were then in effect, I’m probably simplifying, but were fed to the machines cutting the metal – or whatever it is, these things are made of – directly so that they could be built in skipping a lot of modeling. And I don’t – cardboard and clay?
Kristen Baldwin: I think skipping really a lot of the time it takes to manufacture and produce hardware prototypes. So we’re able to do this virtually. You know, digital engineering starts with model-based systems engineering. And we’ve been implementing this for decades now. But what’s really new is today’s instantiation, along with modern data analytics and computing capabilities, creates a transformational opportunity. So as the Air Force and space force fully embrace digital engineering, we’re seeing benefits, such as we’re able to model 1000s of different design concepts early on in acquisition, before a program even starts. And then billions of design trades can be assessed. And if you pair this with artificial intelligence, we have an opportunity for a more optimized system design. And then we can revisit all of that immense data. if something changes later on, like a threat actors capability. We can also do prototyping and developmental testing of systems virtually. Much cheaper than testing the real hardware, and much more quickly. And all of this provides an opportunity for earlier and more frequent analysis, and informs formal hardware evaluations that can reduce surprise in operational test that cause rework today, late in [an] acquisition program lifecycle.
Tom Temin: Now trainers and systems like this you buy from vendors. So is it the Air Force designing this? Or are you working this through the suppliers that actually, you’re buying from that are building this stuff?
Kristen Baldwin: You know our strategy is absolutely to work along with industry. Industry – our defense industry, and certainly our commercial industrial base has been incorporating these technologies and these opportunities. And so our strategy to focus our transformation on program Pathfinders have been a terrific way to make this real for our workforce. And to be able to learn from the benefits that industry is incorporating. Our industrial partners have unique instantiations. And so what the defense department wants to do and what we’re doing in the Air Force is to create a common digital stack of models and infrastructure, so that we can have consistent ways to design an interface with our tools with the data and engage with our multiple defense supply chain actors.
Tom Temin: We’re speaking with Kristen Baldwin, she’s deputy assistant secretary for Science, Technology and Engineering at the Air Force. So in the case of the T-7, Boeing is building it in essentially as the prime contractor. So do you have people in the Air Force and people at Boeing working on common screens with a common software base in the cloud, is that’s kind of how it works in practicality?
Kristen Baldwin: That’s right. That’s the goal. So we have a common infrastructure and set of environments that we’re able to offer through our common Platform One and Cloud One capability, and also our agile software environment. You know, what we talk about here in the Air Force is a digital trinity that brings together the modeling capabilities that I described, and engineering capabilities and digital engineering, along with open architectures, and open standards, where we’re designing our systems using common reference architectures, and making sure that we employ open standards, so that we can offer interoperability and tech refreshed opportunities and really open up competition. And the third leg of the digital trinity is agile software practices. And so within the government, we’re connecting all these three and converging them for a truly transformational change in the way that we do business.
Tom Temin: And some of these principles have been applied to retrofitting certain platforms. I think I read in one release that the new engines hanging on a B-52, for example, or new wings on the A-10 were mentioned. And so here you’ve got an old system, some that might have been designed decades ago, and you’re trying to retrofit it with new. How does that all work when maybe the blueprints don’t even exist anymore for the older, original parts of the platform?
Kristen Baldwin: You know, that’s one of the driving factors is that for some of these very old legacy systems, we don’t have the original design blueprints, the original tech data packages, unfortunately, and so we have to recreate them. But this new digital and computing capability enables us to recreate them in a way that we can actually benefit. And so I’ll talk a little bit about the one that you mentioned. Our A-10 program is in sustainment in one of our organic depot sustainment centers. And they have mastered the art of 3D modeling. They digitized their wing replacement program that was necessary to retrofit these aircraft. And as a result, they’ve cut timelines, returning over 230,000 operational hours to the A-10 fleet, all done by our organic government talent activity. And you also mentioned that we’re able to apply this to programs that might be long standing platforms that we are maintaining, but we’re modernizing them with new technologies like our B-52 commercial engine replacement program. We worked with our supplier and analyzed engine concepts, delivered digital prototypes for candidate engines. And then in the very next month, the engineering team demonstrated digital prototypes using analysis-based videos and virtual, immersive walkthroughs. And then they were able to translate all of that digital technology into 3d printed physical models. The Air Force is rolling out digital engineering and our digital transformation in new programs where they can really be sort of born digital, as well as legacy programs that are being modernized, and older programs that are in sustainment. And each of these instantiations of this transformational technology, we’ll be able to apply the practices in a way that most benefits their particular instance.
Tom Temin: And what’s next on the drawing boards, so to speak?
Kristen Baldwin: So it’s about creating this culture and process and workforce change. You know, we’ve got a lot to learn. But the benefits, as I described, are clearly being seen today. Training a workforce as large and as dispersed as ours is a challenge. But the good news is our younger workforce is clearly ready, and more familiar with model based engineering practices. So we’ll need the continued investment in training in infrastructure, and the tools to fully enable our workforce to get after this digital transformation. But this cultural change is important, too, and this in offices, all of our supply chain, and our governance across the Department of Defense. We’re moving away from current paper deliverables and PowerPoint driven decisions to a more dynamic iterative, digital artifact-based process. It’ll really re-baseline the way we do business today. And so we really look forward to the continued partnership that we’ve got with industry on this journey and advancing our practices so we can continue to fly, fight and win in airspace in cyberspace and do it digitally.
Tom Temin: Kristen Baldwin is deputy assistant secretary of Science, Technology and Engineering at the Air Force. Thanks so much.
Kristen Baldwin: Thank you.
Tom Temin: We’ll post this interview at FederalNewsNetwork.com/FederalDrive. Hear the Federal Drive on demand. Subscribe at Podcastone or wherever you get your shows.
Copyright © 2025 Federal News Network. All rights reserved. This website is not intended for users located within the European Economic Area.
Tom Temin is host of the Federal Drive and has been providing insight on federal technology and management issues for more than 30 years.
Follow @tteminWFED