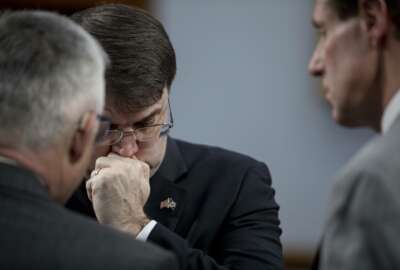
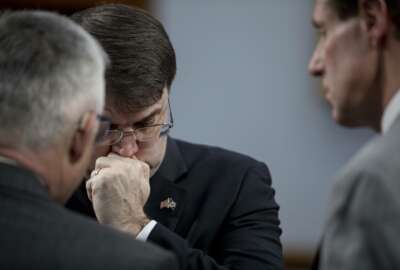
Hubbard Radio Washington DC, LLC. All rights reserved. This website is not intended for users located within the European Economic Area.
Defense Logistics Agency Director of Research and Development David Koch joined the Federal Drive with Tom Temin to talk about a recent contract DLA awarded to ...
Best listening experience is on Chrome, Firefox or Safari. Subscribe to Federal Drive’s daily audio interviews on Apple Podcasts or PodcastOne.
Face masks might be great for preventing germ spread, but they and other personal protective gear can get might gross mighty fast. People breathe, sweat, cough and lord knows what else. Now the Defense Logistics Agency has awarded a contract to develop equipment that can disinfect protective gear. Joining the Federal Drive with Tom Temin, the DLA’s director of research and development, David Koch.
Interview transcript:
Tom Temin: Mr. Koch, good to have you on.
David Koch: Oh, good morning, Tom. It’s so good to be on really glad to be able to share this stuff with you today.
Tom Temin: Now I’m looking at a picture from your press release that looks kind of like a microwave oven. Tell us what you’re trying to accomplish here with equipment that I saw people pretty much used and just threw out and got a fresh one.
David Koch: Yes. Happy to do that. So the machine itself is about the size of a large microwave oven. What we’re trying to do is we’re actually trying to use this technology called cold plasma fog technology. It has been shown to be able to oxidize or kill viruses and pathogens on surfaces. So what we did is we had a company called AA Plasma that was actually doing a Small Business Innovation Research project for us in our subsistence network. So, think of food. And what they were doing was a project on killing and preserving fresh fruits and vegetables using this technology. Well, once COVID-19 kicked off, they immediately came to us and said, “You know, this is a great technology that has application that could potentially be used to kill viruses and pathogens from personal protective equipment.” And so we worked with OSD to secure additional Small Business Innovation Research dollars to be able to give them a contract to be able to pursue producing this to be able to kill germs on PPE.
Tom Temin: And the equipment that they had already developed, does that need to be reconfigured in some manner to be able to use on PPE?
David Koch: Absolutely. So it’s probably a much larger machine that would be used on fresh fruits and vegetables. And this is, as you saw, it’s more of the size of a microwave so it’s more portable. It could be put in an office facility or in a hospital lab where it can be used.
Tom Temin: And cold plasma, that sounds like the opposite of an autoclave which uses heat. What is that technology and how does it work?
David Koch: So I know a little bit about the technology. Dr. Fridman, from AA Plasma is really kind of the genius behind this work. But basically hot plasma would be like lightning, when you see lightning go to the air and it totally you know evaporates everything, that would be hot plasma technology. Cold plasma uses, obviously, a much smaller amount of electricity and water to produce a fog that then kills the viruses. It oxidizes and kills the viruses and pathogens that might be on a surface.
Tom Temin: But it is somehow the discharge of electricity and water and somehow this machine combines all of this to zap something.
David Koch: Right to produce a fog that settles on the goods and kills the pathogens.
Tom Temin: Now this deal that you have with the company is a contract. It’s not a grant and it’s not an SBIR. Why did you choose the contract route? How was that most effective in getting this developed?
David Koch: It is an SBIR contract that we have with them for $1 million dollars to give them the opportunity to prove that they can use this technology to be able to kill pathogens on these products. Their plan is that they’re going to produce three prototypes that are being tested by Drexel University. While they’re doing that, they’re also simultaneously working with the FDA for emergency use authorization. So once Drexel’s finished their testing and the FDA has given them emergency use authorization, then really the next step is that they’re going to produce 100 prototypes to be able to provide the hospitals and frontline care facilities. And I think they have all these already picked out so that they can get the mask, get the 95 mass performance criteria and be able to provide feedback to them on how it worked and if successful, then they’d be able to turn it into production and that would be beyond the research project for them to do that.
Tom Temin: We’re speaking with David Koch. He’s director of research and development at the Defense Logistics Agency, and do you have a sense of how expensive the resulting technology might be? Because, you know, every federal office can afford a microwave. They’re 100 bucks nowadays. I have a feeling those are all going to be gone at some point. And maybe these things will be in their place.
David Koch: That’s funny and probably true. You know, we did ask that question with them, but that will depend on the companies that actually produce it for mass production on what they would charge. I can tell you the actual number of parts and stuff that go into it. It isn’t that expensive to build, but it’s probably a bit more expensive than an industrial microwave that you would see in a work center.
Tom Temin: I guess if you’re supplying a large number of employees with masks all the time, though, it would probably pay for itself in a pretty short order, I guess, is the theory here?
David Koch: I think so. I think that if you use these in smaller labs and care facilities, where maybe you don’t need a larger machine to decontaminate personal protective equipment, this would be perfect. And it would be more in the realm of something that you could afford to put into that office.
Tom Temin: I mentioned face masks in the beginning. What else could they be possibly used to disinfect?
David Koch: So they’re thinking masks, gowns and face shields are probably the primary things. I think the normal size of this, they say, you can put about 30 face masks in there. Or you could put three complete sets–masks, gowns and face shields–from three healthcare workers into the machine. And it can handle either of those at one time. And it’s really pretty quick. I mean, it literally takes five minutes to oxidize, to kill the viruses, and then it takes another 15 minutes for it to dry out. So 20 minutes later, your products are clean and ready to be reused. And of course, I’ll give you the assumption that this is assuming that everything tests out well. This is an R&D experiment.
Tom Temin: Sure. I guess someone has to verify that there are no germs or the viruses that were on the stuff are dead once it comes out of the machine.
David Koch: Absolutely. Yes. And they’re working with different labs to do that, and Drexel University is one of the key labs that they’re working with.
Tom Temin: Got it. It sounds like something that, perhaps, you would not be able to test under normal usage without a microscope or something. And you just want people to be able to have the confidence they put the mask in and when they take it out, it’s safe.
David Koch: Absolutely. So they’ll make sure that the process completely works and has been tested, received FDA approval. Before they send out those 100 prototype units, they don’t want to put something out there that isn’t actually cleaning off the pathogens correctly.
Tom Temin: And while we have you, what other projects related to COVID-19 and the pandemic might the Defense Logistics Agency be working on?
David Koch: Hey, Tom, that’s a great question. Right after COVID-19 kicked off and we all realized that it was going to be a big deal, I quickly reached out to our program managers within R&D–I mean, we’re actually a pretty small group of about 20 people at Defense Logistics Agency–and said, “Hey, do we have any projects that could potentially have COVID-19 applications that we need to be considering now?” One of them that was a completed project was the Joint Additive Manufacturing Model Exchange, or what we commonly call the JAMMEX. And it was developed by DLA and OSD Research and Engineering, basically, at Ms. Lord’s request. She give a directive that the DoD have some kind of interoperable capability for additive manufacturing tech data to be shared among the services. It makes sense. I mean, if you produce something in the Air Force, you know, the Army has the same need for that or the Navy, you would want them to have some kind of exchange where they could get that tech data without having to recreate it on their own. So the JAMMEX does exactly that. The COVID-19 application is really that the services already have access to JAMMEX. They all already use it. So, we uploaded eight models of face shields, surgical masks and face masks that have been clinically reviewed by the VA and approved by FDA. And the value is that, now, each of the services can pull those down, and if they want to organically produce any of that stuff, they’re able to do so.
Tom Temin: Interesting. I see this happening across the government, this type of thing. It’s really amazing how many agencies, large and small, are getting into the act here.
David Koch: Absolutely. That was a great opportunity to use a project that had been recently completed over the past year. We also had another project called Advanced Manufacturing, and it was another transaction authority, which gives us a little bit more flexibility on how we award the contract. But I called it the project at the right place at the right time. We were just awarding it right after COVID-19, so basically in late February. And the whole idea is that you use–instead of the traditional processes–you use Computer Numerical Control or CNC machining. I know you’re familiar with that. But also can use the 3D designs for sheet metal, injection molding, castings, and extrusions. And so they said, “Can you possibly, as the first run of this test, can you see if it’s possible to make face shields?” And we said, “Sure,” reached out to them, and they immediately came back and said, “Yes, we could produce, a batch of 10,000 or more face shields within a couple of days. So it was an R&D experiment, but we produced 11,000 face shields and we shipped them off to New York City first responders. Really the only cost was for them to provide us feedback on how did it work, were they happy with the product, did they receive it timely. Because we want to be able to use it, internal to DLA, to be able to produce some of those parts that we don’t get bids on–they’re more simple to produce, we have the 3D diagrams for them, and see if we can rapidly produce. So, it was a good first test of that.
Tom Temin: So you’re working both in additive and subtractive manufacturing.
David Koch: Yes, yes.
Tom Temin: Sometimes I wonder if the scraps that are removed from one process can be dropped in and become added to another one.
David Koch: Yeah, so true. That’s a good question.
Tom Temin: Well, that’s for another time. David Koch is director of research and development at the Defense Logistics Agency. Thanks so much for joining me.
David Koch: Oh, you’re certainly welcome. Thank you for having me on today.
Copyright © 2024 Federal News Network. All rights reserved. This website is not intended for users located within the European Economic Area.
Tom Temin is host of the Federal Drive and has been providing insight on federal technology and management issues for more than 30 years.
Follow @tteminWFED