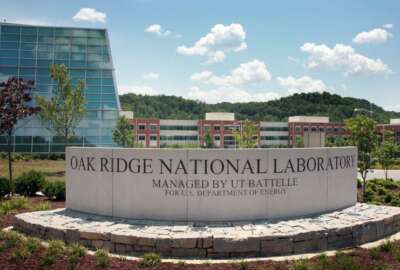
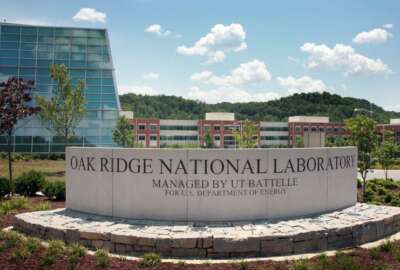
Hubbard Radio Washington DC, LLC. All rights reserved. This website is not intended for users located within the European Economic Area.
Cars, planes and boats will be stronger and longer lasting thanks to a new metal alloy developed by scientists at the Oak Ridge National Laboratory.
Best listening experience is on Chrome, Firefox or Safari. Subscribe to Federal Drive’s daily audio interviews on Apple Podcasts or PodcastOne.
Cars, planes and boats will be stronger and longer lasting thanks to a new metal alloy. It was developed by scientists at the Oak Ridge National Laboratory. Here was what they did and how they did it. Program manager Allen Haynes and research and development staff member, Alex Plotkowski joined the Federal Drive with Tom Temin.
Interview transcript:
Tom Temin: And I guess my first question is a development of an alloy. Why would that happen, say at the lab, how did that happen to occur there versus industry that actually needs these things, Alex Plotkowski?
Alex Plotkowski: So in order to kind of develop these new alloys, these better properties are necessary to really dig deeply into the science and metallurgy around the development of those alloys. And so by doing this at the National Lab, we can use some of the tools that are available to us, that aren’t available to industry. We also have a collection of expertise here for all the things that we need in order to design these new alloys in a way that’s not always accessible to industry. And so we do some of that, that early groundwork and develop these new things. And then it’s our job to take that to industry and help them industrialize it.
Tom Temin: And how did this germinate in the first place? There’s a need for structural alloys in transportation. Is that the basic problem here?
Alex Plotkowski: Yeah, that’s exactly right. So it trends for increased efficiency for automotive and aerospace and other types of applications are going more and more towards these lighter weight alloys. We like aluminum, because it’s lightweight, and it’s corrosion resistant, but we don’t like it because the properties are not quite as strong as steel, for example. And it doesn’t operate as well at high temperatures. And so those are the kinds of problems that we’re out to solve. And if we can figure that out of which we think we have is to be able to design these new alloys and processes that allow us to have these better properties, then we can start to display some of those materials that are heavier, and that lets us get to lighter weight and higher efficiency.
Tom Temin: And Allen, maybe tell us about some of the infrastructure at the lab that enables you to do this work, you must have ovens and I don’t know, you tell me?
Allen Haynes: Yeah, actually, the DOE National Laboratory network is specifically missioned and resourced to steward what we call big science tools. So we do have the ovens we do have the tensile testing, we do have your standard microscopy and Millers tools. But the labs also sponsor very large one of a kind facilities like the spallation neutron source in Oak Ridge National Lab, and the advanced photon source which is which is a synchrotron X -ray facility at Argonne National Lab, and the advanced world class microscopy tool sets, Pacific Northwest National Lab and Oak Ridge National Lab, all of those were brought to bear on this particular problem. And those are tool sets that are too large, too expensive for industry to be expected to practically own and then additionally to also own the staff expertise that can keep those tools operating at the world class pace that they deserve, with billions of dollars of investment. So in the case of this program, the program which comes out of the vehicle technologies office of the Department of Energy had the vision to capture those unique sets of material science tools that the national laboratory network owns, stewards for the U.S., and apply those to the development of critical materials problems in order to more rapidly develop solutions. So these are, this is an accelerated program. So our goal is to move the typical materials development cycle from 10 to 20 years, which has been historically what it’s taken to develop a new material, down to a fraction of that, in this particular case, this alloy, one of the interesting subtexts of the story here is this concept. For this printed high temperature, high strength fatigue resistant, pre persisted aluminum alloy, went from an idea on a piece of paper to a full scale prototype test in only 33 months, and pair that to most materials having taken 15 to 20 years to get to that stage, so that’s what the DOE network allows with their massive material science tool sets.
Tom Temin: The implication is that the development of new alloys is a high tech function itself. It’s not mixing things and hammering at them after they harden type of process anymore, is it?
Allen Haynes: No, no. Materials development is very complex. And you’ve got so many features that you have to simultaneously satisfy. You need high strength, you need corrosion systems, we need great resistance, it needs to be manufacturable. It ultimately it needs to be affordable and manufacturable to scale. In some cases, there are trade-offs. Oftentimes, if you go to a higher strength alloy you give up some of the ductility that’s necessary. If you go to higher strength, sometimes you trade off corrosion. So we’re constantly playing this very complex game of trading properties and features as we aim for compositions and processing sectors that give you the desired properties that can also be manufactured.
Tom Temin: And you mentioned that this new material called DuAlumin-3D; that’s a really cool name, is printed. That is to say it’s not cast, it’s not extruded, it’s not molded, and so on, the way metal normally is, Alex?
Alex Plotkowski: Yeah, that’s exactly right. And so when you’re designing an alloy or when we’re manufacturing those things, the properties that you get are a function of both the chemistry, the composition of that alloy, as well as the manner in which you process it. And one of the key things that determines processing characteristic for these types of alloys is the cooling rates that we see during processing. And so casting is a relatively slow process in that respect. Whereas 3d printing actually gives us extremely high cooling rates. And so that gives us a really unique structure to the alloys that you don’t get with other types of processing routes. Now, if you take that and you apply it to conventional alloys, you might be able to achieve kind of the similar types of properties that you get with other processing routes. So the unique thing here is that we’re designing the alloys specifically around those characteristics of the process, which is what enables us to achieve those higher properties, those things that we’d like so much about this particular alloy.
Tom Temin: We’re speaking with Alex Plotkowski and Allen Haynes. They’re both with the Oak Ridge National Laboratory. And let’s talk about the material itself for a minute. Again, DuAlumin-3D, what what is in it besides aluminum?
Alex Plotkowski: Yeah, so it’s quite heavily alloyed with a variety of other elements. In this case, we’re using a combination of cerium, nickel, manganese, and zirconium. And those elements are not just chosen arbitrarily, each one of them serves a particular purpose within the microstructure for that material. And they interact with the processing that we apply to it in various ways as well. And so the pathway to this particular alloy requires us to understand how all those different elements serve their purpose within alloys, and how they interact with each other as well.
Tom Temin: And are these elements generally available in the Western Hemisphere?
Alex Plotkowski: Yes, for the most part, cerium is an interesting one. It’s a rare earth metal. However, it’s it’s not like say neodymium, which is very expensive and high value. Cerium is actually the most abundant, abundant rare earth metals in the Earth’s crust. However, it doesn’t have a lot of practical industrial uses. So for the most part, it’s a byproduct of mining for these rare earths. And so the very early days of this project, we actually took inspiration for another project that was at ORNL, that was looking at casting aluminum cerium-based alloys, the intent being to to purposefully utilize cerium in a high volume way to help this stabilize those supply chains for those higher value products. Other than that, the other alloying elements that we’re adding are fairly conventional with respect to use in various aluminum alloys. And it’s just important that we’re mixing them in the right way at the right proportions, and then processing them appropriately.
Tom Temin: All right, and then you mentioned commercial and industry, what is the route by which this gets into commercial use? Because it sounds like industry would have to develop new processes and have new equipment to be able to produce this at scale, economically for use in cars and planes and boats or whatever else.
Allen Haynes: You’re exactly right. This does. The work that’s done at the National Labs, is intended to be handed it off to industry. And in the particular case of this alloy, we’ve worked closely once alloy was developed, we work closely with General Motors, and then a company called Beehive 3D. In order to scale the concepts that were demonstrated at the lab to industrially compatible processes. The 3d printing is still in the early stages, it’s still lower TRL in many cases, but industry is slowly beginning, the automotive industry particularly, slowly beginning to find key applications. In most cases, it’s going to be small, niche applications in the near term. So the value of 3d printing is that you can either provide complex geometries that are possible via other manufacturing routes, or in this particular case, you can also manipulate microstructures, which is the structure of the material internally to provide properties that aren’t achievable by other routes. And if you can do both, which in this case you can, now you have a value equation that perhaps trumps the cost of having to adopt new processes and adopt higher cost materials. The trade-off in our case for this material is it is a higher cost material doesn’t compete from a cost perspective with raw cast materials, with the properties advantages it offers, have apparent value that will trump the cost difference. So that you know, some process that’s iterative, it’s there’s no formula for this, to be able to transition to a deployable technology. But GM has adopted this, and is considering it will be testing full scale pistons from this material in one of their newest lightweight engines for SUVs in the year ahead.
Tom Temin: So it doesn’t have to be painted this particular material?
Allen Haynes: No, this particular material does not have to be painted. It’s in an engine, it will be operating at very high temperatures under very extreme combustion conditions, which allows those engines to provide higher efficiencies. And even as we’re transitioning to an electrified future, which we’re certainly supporting that and all in all there’s still going to be a need for hybrid vehicles, where you’ll have some combustion during this transition period, particularly. And these alloys can definitely support that hybridization stage of the transition to electrify transportation.
Tom Temin: Allen Haynes and Alex Plotkowski are scientists with the Oak Ridge National Laboratory.
Copyright © 2024 Federal News Network. All rights reserved. This website is not intended for users located within the European Economic Area.
Tom Temin is host of the Federal Drive and has been providing insight on federal technology and management issues for more than 30 years.
Follow @tteminWFED